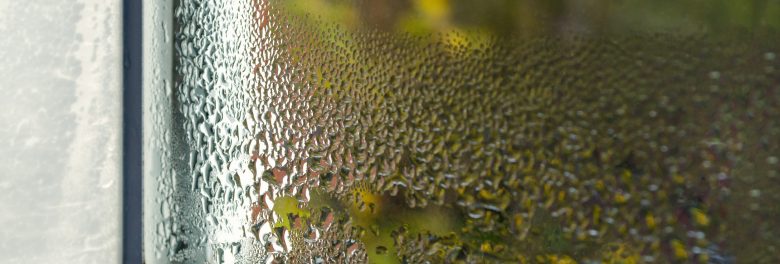
A more detailed assessment of surface condensation risk can assist in minimising risk of mould growth and maximising construction quality. In high risk areas, particularly around window frames and bathrooms, it is important to make sure that the humidity is considered to reflect a range of real-life scenarios – so a more detailed methodology that accounts for varied environmental scenarios must be used. This will ensure that the construction is not prone to condensation and that the residents enjoy a healthy environment.
Condensation usually occurs near building junctions due to cold spots resulting from the thermal bridging effect, where the lower temperatures make droplets appear. These conditions include internal and external temperature assumptions, paramount to calculate where the cold spots will form inside the building. It is also important to account for the internal humidity, since the more humid the air is, the more likely it is that droplets will form in these spots.
These conditions reflect real life scenarios. In winter, for example, where the internal-external temperature difference is high, condensation is much more likely to occur if humidity levels are also high. During summer, the risk is diminished.
However, not all surface condensation risk methodologies allow for this. For example, the BRE guidance (BR497) does not use humidity levels for assessing the condensation risk, and is very strict with the temperature assumptions. This type of assessment is usually an output from psi-value calculations, but it may not be enough for the whole picture, sometimes being questioned by building control.
Posted on October 22nd, 2020
Author: Rodrigo Guedes
Related services: Condensation & Moisture Management,