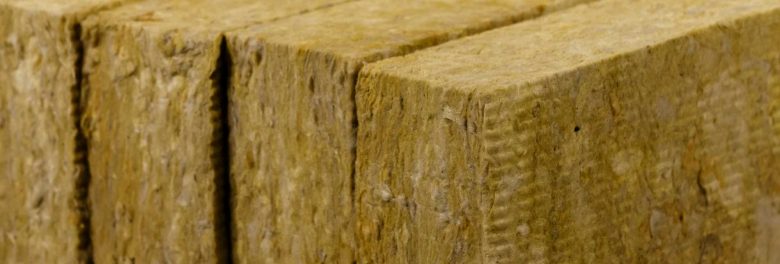
It’s not an easy switch to mineral wool to address pipework corrosion risk caused by phenolic insulation.
On Low Temperature Hot Water (LTHW) systems the thickness of mineral wool required to achieve the same insulating properties may be considerably more than you think. For example, more than 1.5 times the insulation thickness may be required when using mineral wool compared to phenolic insulation, as illustrated in the figure below. While this may not have significant cost impact, it is important to consider on site constraints such as proximity of the pipework to other equipment or services and space restrictions within risers and laterals.
Phenolic insulation is susceptible to decay and causes pipework corrosion when it gets wet. Therefore, measures should be taken to prevent water ingress. Pipework should be properly installed to avoid leaks and all welds should be painted with corrosion resistant paint prior to joint insulation and casing work. The insulation should have an integral moisture barrier to prevent the foam from getting wet. Breaks, penetrations, or damage to the foil face should be avoided. This is in line with CIBSE CP1 which states that insulation shall be continuous and close fitting at all joints and include a vapour seal.
Posted on April 7th, 2021
Author: Carlyne Parillon
Related services: O&M Tendering & Tariff Modelling, ESCO Tendering, Masterplanning & Strategy, Design Stage, Construction Stage,